PPR pipe Production Process
- Share
- publisher
- Eve
- Issue Time
- Aug 23,2024
Summary
PPR pipes are widely used in hot and cold water systems, underfloor heating, and potable water supply due to their excellent thermal stability, corrosion resistance, and high pressure tolerance.
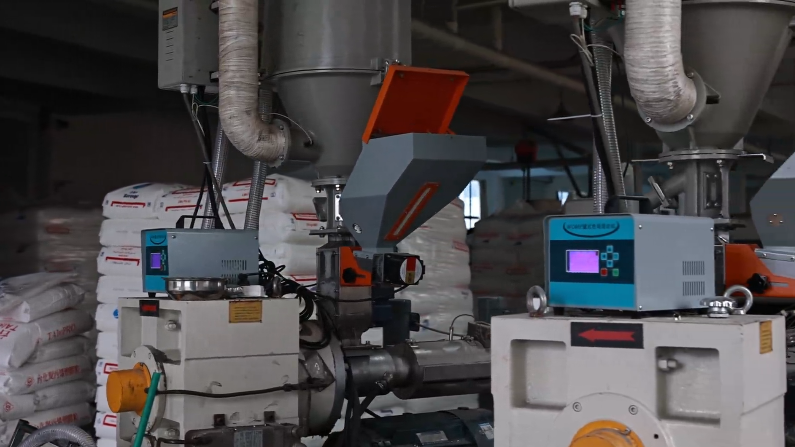
PPR pipe Production Process
Raw Material Preparation
The production of PPR pipes starts with high-quality polypropylene raw materials. These materials are typically made from a random copolymer of polypropylene, which offers good chemical stability and mechanical properties. During the production process, the raw materials are first dried to remove any moisture that might be present, ensuring the quality and consistency of the final product.
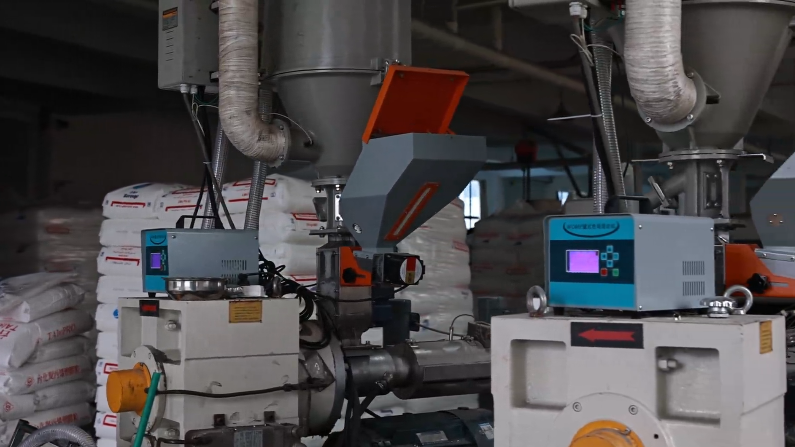
Extrusion Molding
The dried PPR raw materials are fed into an extruder for melting. The extruder uses heat and rotating screws to melt the raw materials into a uniform molten state. The molten PPR is then extruded through a mold to form a continuous tubular structure. The design and precision of the mold play a crucial role in determining the final dimensions and quality of the pipes.
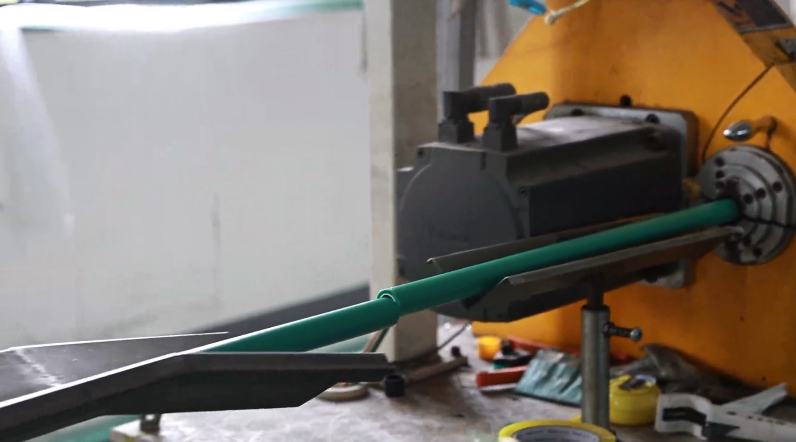
Cutting and Inspection
The cooled and shaped PPR pipes are then transported to a cutting machine for length cutting. The cut pipes undergo rigorous quality inspections, including visual checks, dimensional measurements, and mechanical performance tests. Only pipes that pass all inspections are packaged and sent to the market.
Conclusion
The production process of PPR pipes involves several steps: raw material preparation, extrusion molding, cooling and shaping, and cutting and inspection. Each step requires precise control and strict oversight to ensure the final product has superior performance and reliability. By understanding these production processes, one can better appreciate why PPR pipes perform exceptionally well in various applications.