Comparison of Advantages and Disadvantages of HDPE and PVC
- Share
- publisher
- Eve
- Issue Time
- Aug 23,2024
Summary
Electrofusion fittings are essential pipe connections, and their manufacturing process directly impacts the quality and performance of the products. In this article.

Manufacturing Process of Electrofusion Fittings
Electrofusion fittings are essential pipe connections, and their manufacturing process directly impacts the quality and performance of the products. In this article, we will detail the manufacturing process of electrofusion fittings and discuss the key elements of each stage.

Material Preparation
The manufacturing of electrofusion fittings begins with the selection of high-quality HDPE (High-Density Polyethylene) material. HDPE material is known for its high strength, corrosion resistance, and excellent heat fusion properties.
Selection of HDPE Material: Using the latest HDPE PE100 material ensures the durability and reliability of the fittings.
Cleaning of Material: The material needs to be thoroughly cleaned before production to remove surface impurities and ensure welding quality.
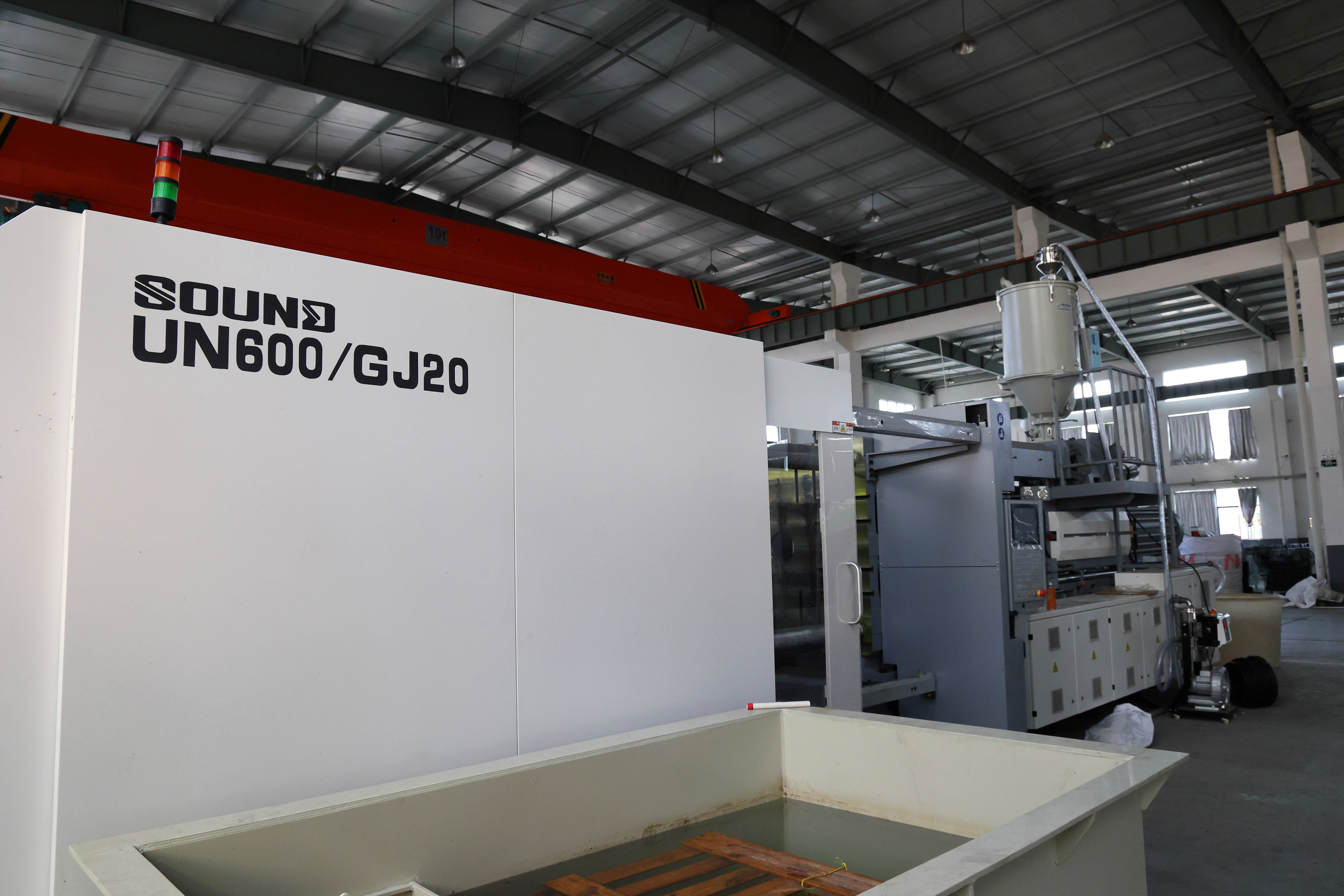
Production Process
The production process of electrofusion fittings is crucial to ensuring their performance and quality. The entire process includes molding, welding, and cooling steps.
Molding: Advanced injection molding equipment is used to inject HDPE material into molds, forming the basic shape of the fittings.
Welding: Electrofusion welding technology is used to connect the fittings with electrofusion joints. This process requires precise control of temperature and time to ensure welding strength and sealing.
Cooling: After welding, the fittings need to be naturally cooled to avoid the impact of thermal stress.
Quality Inspection
To ensure the quality of electrofusion fittings, strict inspections are carried out, including appearance checks and performance tests.
1. Appearance Check: Inspect the fittings' surface for defects such as bubbles and cracks.
2. Size Measurement: Use professional tools to measure the dimensions of the fittings, ensuring they meet standards.
3. Welding Strength Test: Conduct tensile tests to assess the strength of the welded parts.